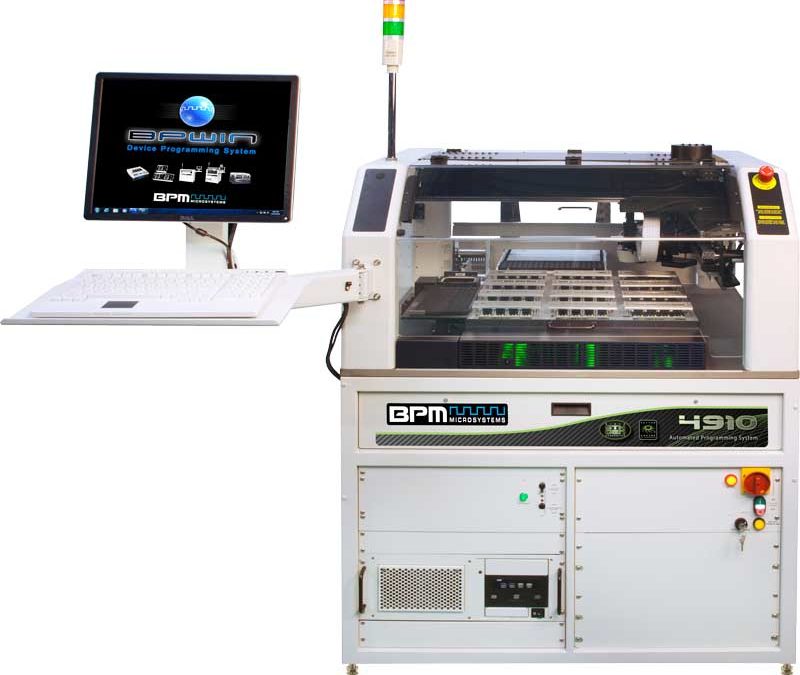
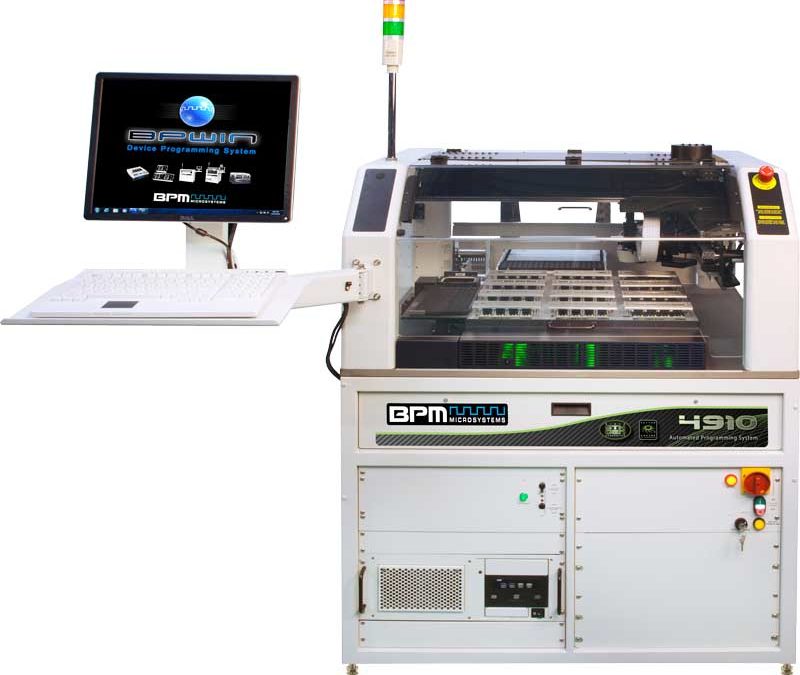
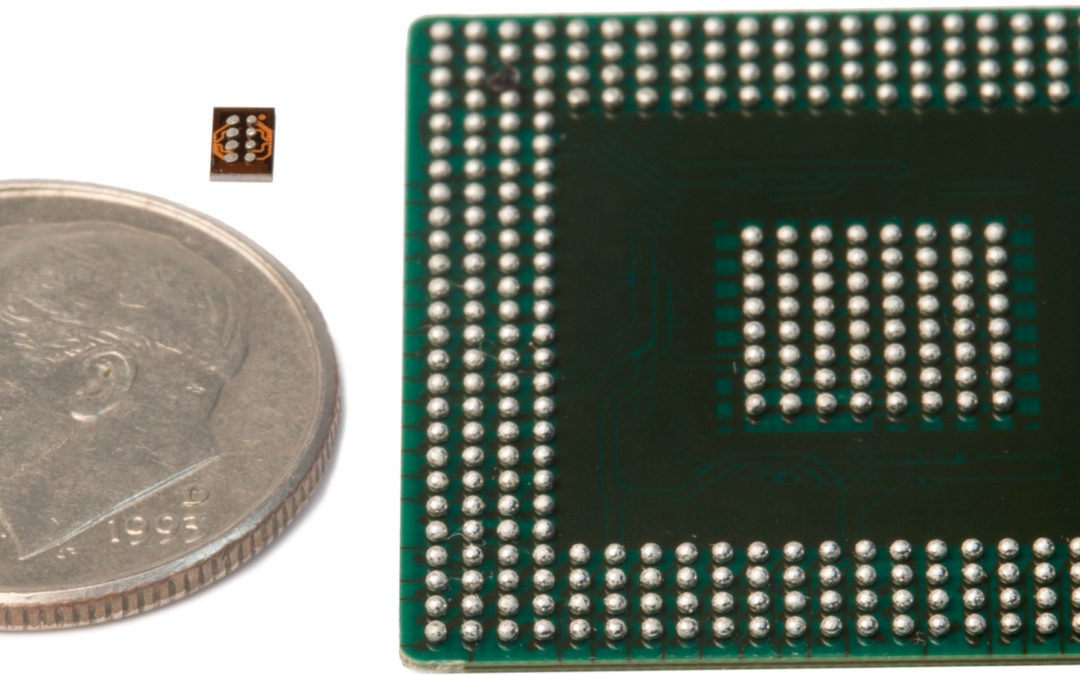
Device Support Lead Time Update
BPM is pleased to update the estimated support lead times for a variety of devices
BPM has nearly doubled the engineering staff in Device Support in the past year. We have more resources than we’ve ever had and adding even more team members. This is helping to reduce lead times for new device support requests (DSRs). We’ve also segmented support by device type and complexity. The following chart breaks it down:
Algo Device Support Request by Device Type | Algo Lead Time |
Simple Update: | 5 Days |
Package Addition: | 2 Weeks |
NOR Flash, Serial NOR Flash, EEPROM, Serial EEPROM, Parallel EEPROM, Raw NAND, eMMC, HS200 or HS400 eMMC, Simple PLD: | 4 Weeks |
Simple Microcontroller, Standard Microcontroller: | 4 to 8 Weeks (depends on complexity) |
Complex PLD, Actel Flash, Actel Antifuse: | 8 Weeks |
Raw NAND with BBM, Complex Microcontroller, FPGA, BBM Scheme, Complex Xilinx Antifuse: | Requires Research to Quote |
BPM currently supports over 70,000 devices from over 200 manufacturers. For the supported device search, click here.
Current BPM customers get free Algorithm Support Credits (up to six $500 credits) for new support with a current Software Agreement. Manual production programmers get four algorithm credits; Automated Programmers get six algorithm credits, good for one year. You can learn more here. To request new device support with faster device support lead times, click here.
Support Agreement
BPM’s production level support agreement is designed for those customers who run critical operations and demand the highest level of support possible, and includes the following:
- 24/7 Hotline: +1 832-617-5702
You can report issues with device production outside of normal business hours. The customer will be put into contact with a live Field Service Engineer (for APS-related issues) or Customer Service Engineer (for device-related issues). Engineers will work with customers to collect all data on the issue, provide debug steps to resolve the issue over the phone, and will immediately create a BPM case if the issue requires additional time to resolve. This service is available to any BPM customer located in North America (Canada, the US, and Mexico). Fees apply if not covered by the current service/software contract. - Spare Parts
Warranty replacement parts can ship from our headquarters in Houston, Texas, or directly from one of our global stock locations. Warranty replacement does not cover consumable parts or damage caused by the customer. In the case of local spare parts, customers have had replacement parts at their facility installed in less than 30 minutes. - Priority Case Handling
You will receive priority in our new customer relationship management system. All of your incoming cases will receive a special tag that designates you as a full support user and we will prioritize your requests as necessary. - On-Site Support
On-site support does not require a PO for labor hours when you are under a hardware contract.
If you would like to learn more about BPM or have a service or technical-related question, please call +1 (713) 688-4600, toll-free in the US at (855) SELL BPM, or 24/7 Service hotline at +1 (832) 617-5702. You can also email technical support at tech@bpmmicro.com.
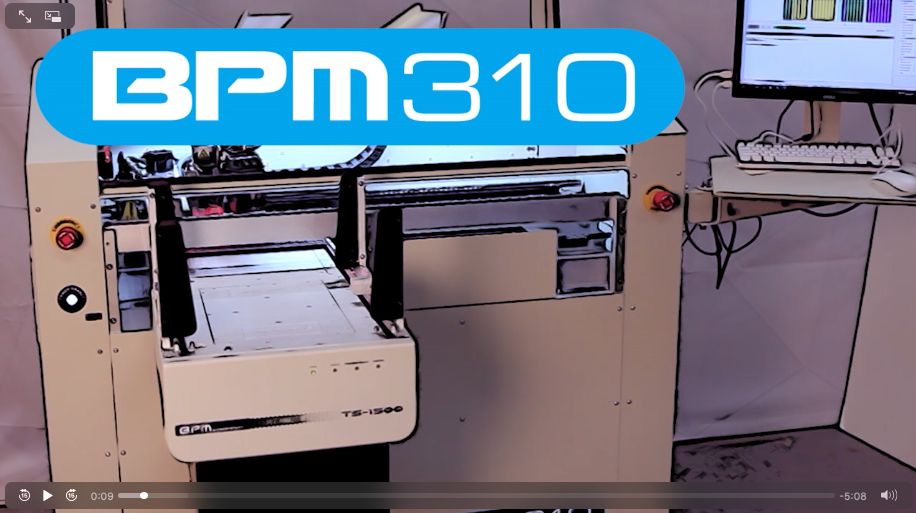
BPM310 Automated Programmer Video
BPM310 Automated Programmer Video The BPM310 Automated Programming System– the first 10th Generation programmer offers the industry’s fastest programming times for UFS, eMMC, Flash, and MCUs with twice as many sockets per site as its predecessor. The BPM310 offers a...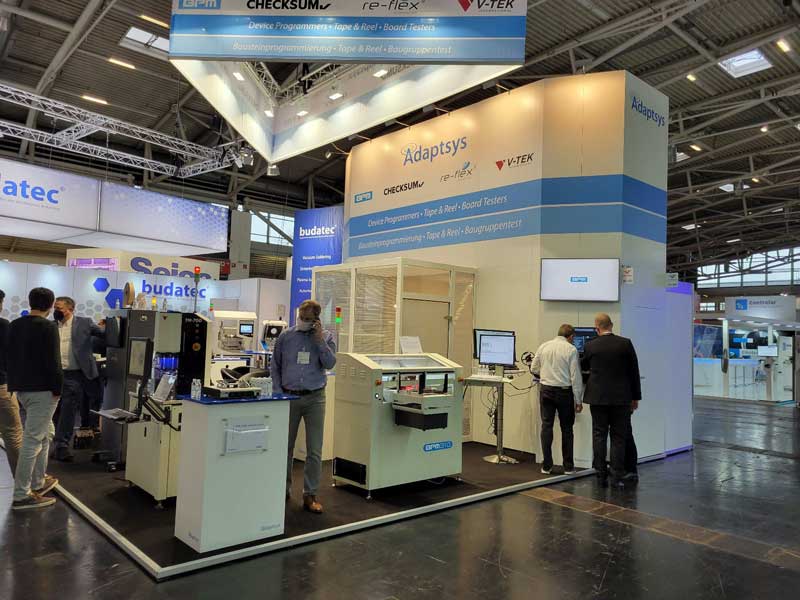
Productronica Day One
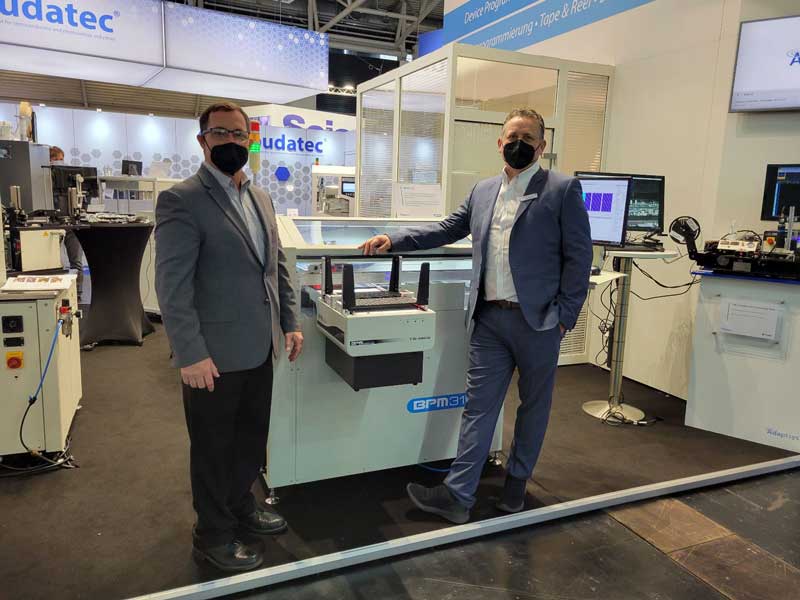
Colin Harper, BPM’s Global Sales Director, and James Cawkell, BPM’s Distributor in Europe, show off the latest APS from BPM, the BPM310.
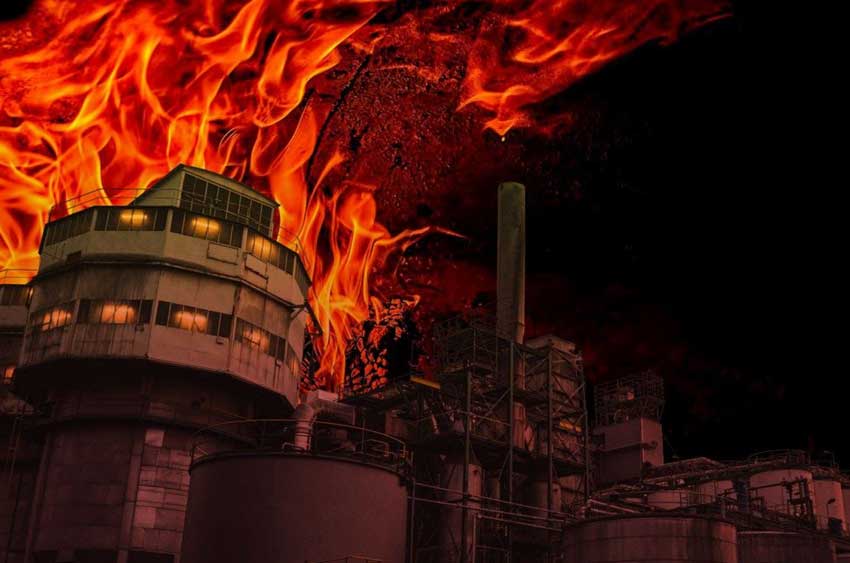
Disaster Recovery for a Modern Manufacturing Operation
Some things to consider in a Disaster Plan
- Hardware/Software contracts are up-to-date
- Ensures the fastest response in line-down situations
- Spares are on-site and/or available overnight
- Schedule deliveries for consumables, especially sockets
- Sockets are consumable items
- The schedule ensures they are manufactured/delivered based on your requirements
- Lead time to build a socket can vary, from days to weeks
- Multiple prequalified vendors
- Pre-qualify First Articles ahead of time from your partner supplier
- Negotiate price per device before the disaster takes place
Some problems are good. It’s important for the modern manufacturing operation to prepare for the worst, and the best. There are lots of things that can go wrong. Add this to the list: what happens if one or more people on your line come down with Covid-19? You still have parts to program and production lines to supply. And as things rebound, what will you do if you are hit with an increase in orders? You (no doubt) have built-in capacity; but what if it doubles, or triples (or more)? BPM Microsystems builds systems and accessories that make it easy and cost-effective to make device programming a viable (and profitable) option in-house. Their line of programmers is universal, meaning they utilize the same software and accessories, from the smallest to the largest systems. From the first article (the initial first approved programmed device) to production, the only difference is throughput. Manual systems are perfect for starting out and/or smaller lot sizes (up to 50,000 parts per year). They also come in handy to augment the automated system’s capacity, or for programming short-run parts. BPM’s automated systems are the fastest and easiest to set-up of any programming systems. They are made for programming large data devices, such as eMMC HS400, NAND, NOR, and Serial Flash devices, and other nonvolatile memory devices such as MCUs, PLDs, and FPGAs. High-speed signals support devices up to 200 Mhz and the latest eMMC HS400 modes with data transfer rates of 2.5 nanoseconds per byte. With data transfer rates to 50 Gb per second, and verify rates up to 200 MB per second, BPM’s Automated Systems offer the industry’s fastest times. This is up to 9 times faster than competing “universal” programmers, offering the Largest Memory Support in the industry―256 GB, upgradeable to 512 GB.
WhisperTeach™ & CyberOptics™
WhisperTeach™ is patented hardware/software that automates the critical z-height measurement, which reduces set-up times by as much as 83%. More importantly, it improves yield and job performance compared to manual teaching methods. CyberOptics™ vision component auto measure delivers on-the-fly alignment to maximum device reliability and throughput.
Learn more about WhisperTeach™ auto Z-height teach system here.
Add Capacity
Adding capacity is fairly straightforward. The first option is to add overtime and/or add shifts. BPM’s set-ups don’t require extensive training, so quality and throughput won’t decline after 5 pm. Next, add programming sites and sockets to existing workflows. If utilizing manual systems, additional programmers can be “daisy-chained” to a single workstation (up to 12 total). For automated programmers, additional sites may be added. Each site has the ability to add up to 4 additional sockets (a socket is the electrical interface of hardware/software to program a specific device). Adding sites can double, triple (up to 10X) capacity, depending on which system is used. BPM’s universal sites mean you don’t need two different site technologies for programming different classes of devices. BPM supports more than triple the number of devices as their nearest competitor (36K vs 12K). Some BPM systems, such as the low-cost 3901 or 8th Generation automated systems, can be upgraded for higher throughput, with more devices per hour and/or additional sites or peripherals. When you experience a line-down (for whatever reason), you need solutions that allow you to quickly shift production without skipping a beat. For programming devices, contact your nearest programming center, such as Arrow, Avnet, or A&J. The set-up files can be securely transmitted; if they don’t have the sockets, simply overnight the sockets used on your production. Utilizing programming centers is another way to balance out your work-flow; when a temporary need overwhelms your workflow, you can outsource for extra capacity.
Conclusion
It’s not a matter of “if” things go wrong. It’s a mathematical certainty. If 2020 has taught us anything, it’s prudent to be ready for just about anything. With a little forward planning, you should keep production moving. BPM’s systems are built to grow with your business; they have programmers that are still operating daily after 15 years or more. Contact your preferred Programming Center and BPM Microsystems to develop a disaster plan in advance.
See “Market Forces” Article here